Разработан новый процесс полимеризации
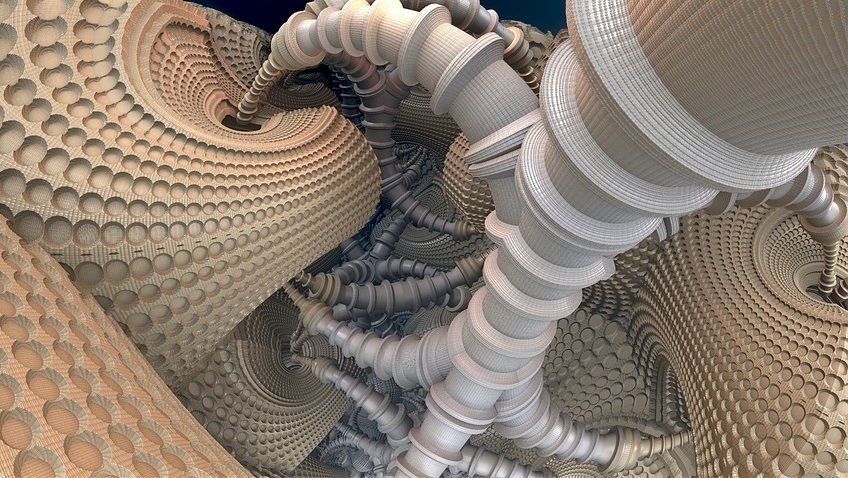
Производители автомобилей, самолетов, автобусов — все, кто нуждается в прочных, легких и жароустойчивых деталях — готовы извлечь выгоду из нового производственного процесса, который требует только быстрого контакта с небольшим источником тепла для отправки каскадной закаливающей волны через полимер. Исследователи из Университета штата Иллинойс разработали новый процесс полимеризации, который может снизить затраты, время и энергию, необходимые по сравнению с текущим производственным процессом.
В выводах, представленных в Nature, говорится, что новый процесс полимеризации использует на 10 порядков меньше энергии и может сократить два порядка величину времени в течение текущего производственного процесса.
«Эта разработка знаменует собой то, что может стать первым крупным достижением в области высокопроизводительной полимерной и композитной обрабатывающей промышленности почти за полвека», — сказал профессор аэрокосмической техники и ведущий автор исследования Скотт Уайт.
«Материалы, используемые для создания самолетов и автомобилей, обладают отличными тепловыми и механическими характеристиками, но процесс изготовления дорог с точки зрения времени, энергии и воздействия на окружающую среду», — сказал Уайт. «Одна из наших целей — сократить расходы и увеличить производство».
Возьмем, к примеру, сборку воздушных судов. По словам Уайта, для одного крупного производителя США процесс производства только одной части крупного коммерческого авиалайнера может потреблять более 96 000 киловатт-часов энергии и производить более 80 тонн CO2, в зависимости от источника энергии. Это примерно такое количество электроэнергии, которое требуется для обеспечения девяти средних домов в течение одного года.
«Производители авиалайнеров используют печь для отвердения диаметром около 60 футов и длиной около 40 футов — это невероятно массивная структура, наполненная нагревательными элементами, вентиляторами, охлаждающими трубами и всякими другими сложными машинами», — сказал Уайт. «Температура повышается примерно до 350 градусов по Фаренгейту в серии очень точных шагов в течение примерно 24-часового цикла. Это невероятно энергоемкий процесс».
Исследователи предложили, чтобы они могли бы контролировать химическую реактивность для экономии процесса полимеризации. «Существует много энергии, хранящейся в химических связях смолы, чтобы подпитывать процесс», — сказал Уайт. «Научиться высвобождать эту энергию с нужной скоростью — не слишком быстро, но и не слишком медленно — было ключом к открытию».
«Прикоснувшись к тому, что является, по существу, паяльником, к одному углу полимерной поверхности, мы можем начать каскадную волну химической реакции, которая распространяется по всему материалу», — сказал Уайт. «После срабатывания реакция использует энтальпию или внутреннюю энергию реакции полимеризации, чтобы продвинуть реакцию вперед и осуществить полимеризацию материала».
«Вы можете экономить энергию и время, но это не имеет значения, если качество конечного продукта не соответствует стандартам», — сказал Уайт. «Мы можем увеличить скорость изготовления, вызвав реакцию затвердевания, но ее нужно тщательно контролировать. В противном случае место встречи двух реакционных волн может стать тепловым всплеском, что может привести к ухудшению характеристик материала со временем».
Команда продемонстрировала, что эта реакция может производить безопасные высококачественные полимеры в хорошо контролируемой лабораторной среде. Они предусматривают процесс, способствующий крупномасштабному производству из-за его совместимости с широко используемыми технологиями изготовления, такими как формование, импринтинг, трехмерная печать и настойка смолы.
Больше информации: Rapid energy-efficient manufacturing of polymers and composites via frontal polymerization, Nature (2018). nature.com/articles/doi:10.1038/s41586-018-0054-x